WELDING OF POLYMER BELTS
START-UP Company offers edge, profile, and partition welding services for polymer belts using modern equipment at competitive prices and within clearly defined timelines.
Belt construction with edges, profiles, partitions, and chevron coatings is designed to prevent material slippage from the belt (the corrugations prevent the material from moving against the direction of the conveyor).
Areas of Application
Food industry (confectionery, bakery, meat processing, and others)
Agriculture
Logistics and packaging lines
Chemical and pharmaceutical industry
Paper and cardboard / drywall production, etc.
Operating Conditions
Horizontal and vertical material transport at angles from 0° to 90°
Product Features
Artificial materials or those with a high level of bulkiness
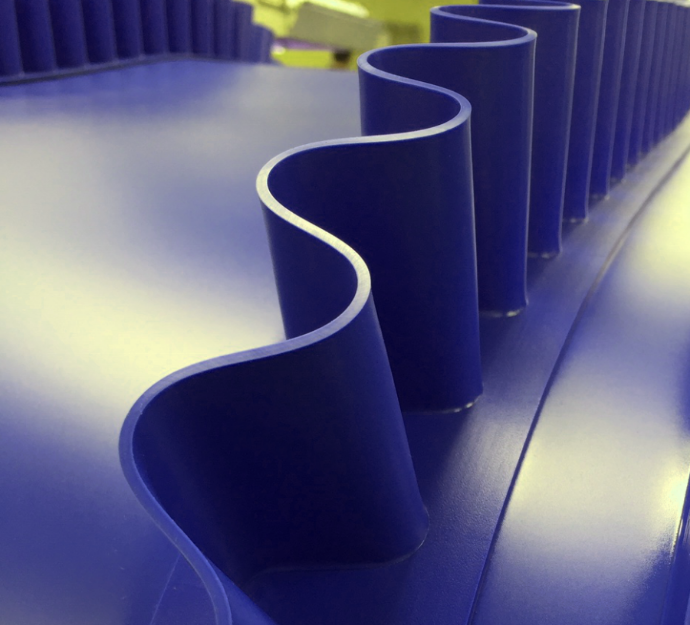
Technical Features
The process of equipping conveyor belts with edges, profiles, and partitions is similar to metal welding. However, in the case of PU and PVC belts, polymer welding is used, ensuring the strength and reliability of the attachment.
The versatility of our equipment allows us to weld edges, profiles, and partitions to the belt at any location, with any pitch.
Our specialists can equip belts with partitions and profiles in various configurations and sizes:
T-shaped partitions 90°: 20 mm
T-shaped inclined partitions 60°: 30, 40, 50 mm
V-shaped and trapezoidal guide profiles: 6x4 mm, 8x5 mm, 10x6 mm, 13x8 mm, 17x11 mm
Square profiles 10x10 mm
Longitudinal edges: straight and S-shaped (corrugated edges): 30, 40, 50 mm
Edges, profiles, and partitions of other types are available upon request
What information is required from the customer?
Length and width of the belt
Diameter of the rollers that the belt will pass over
Material type – PU, PVC, silicone, polyolefin, etc.
What product is being transported?
Total weight on the conveyor
Environmental and Product Characteristics (temperature, humidity, oil resistance, etc.)
Belt speed
Belt support – table or rollers?
If guide profiles are required, specify size and placement
If edges are required, specify type (straight or corrugated), size, and placement
If partitions are required, specify size and placement
WELDING OF POLYMER BELTS
An important part of the process in industrial production is conveyors and conveyor belts. Their regular inspection and maintenance are key to ensuring the continuous operation of the entire production system. The conveyor belt performs a continuous loop, which can be interrupted if damage occurs at the splice or joint of the belt.
Splicing Methods:
Hot Vulcanization (Portable press-vulcanizer with air cooling)
Mechanical Connection (ALLIGATOR brand locks by FLEXCO)
Areas of Application:
Food industry (confectionery, bakery, meat processing, and others)
Agriculture
Logistics and packaging lines
Chemical and pharmaceutical industries
Paper and cardboard/gypboard production, etc.
Service Location
We provide polymer belt splicing services both at our service center and on-site at your production facility.
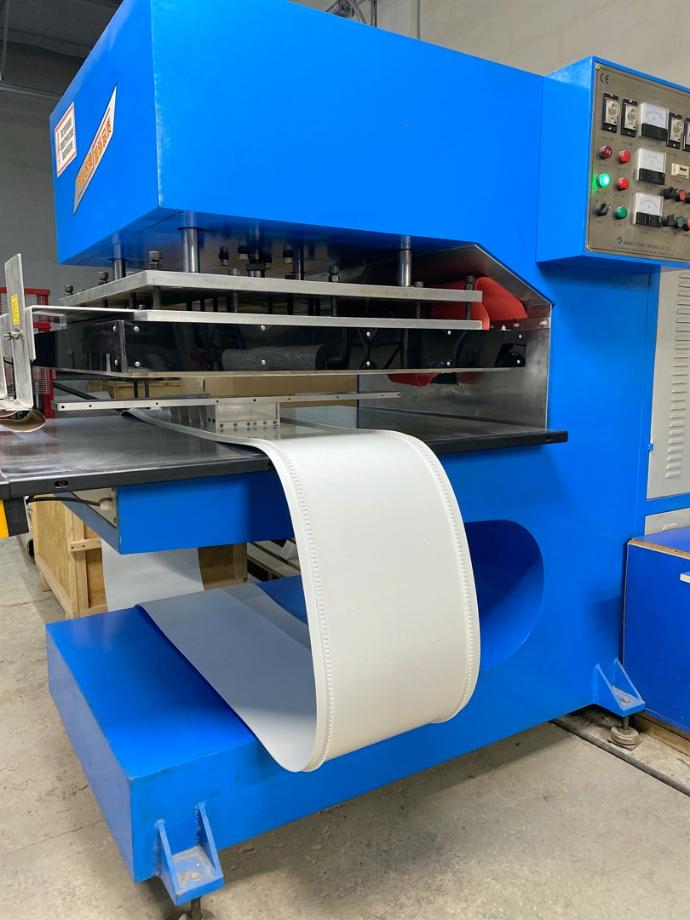
Advantages of Splicing Using Hot Vulcanization Method (Portable Press Vulcanizer with Air Cooling)
The hot vulcanization technology ensures a reliable and strong bond even when the conveyor belt is used in heavy-duty conditions. The process includes melting and hardening the material in the press to eliminate any gaps, forming a continuous layer of the conveyor belt material. This splicing method can be performed under any conditions, regardless of ambient temperature—whether in dusty production areas, high humidity, or low temperatures. The conveyor can often resume operation almost immediately after hot vulcanization.
STRENGTH:
The splice strength is guaranteed to be up to 90% of the tensile strength of the belt, ensuring the durability of the spliced joint.
QUALITY:
Uniform belt thickness, no gaps on the surface of the belt, and high flexibility of the splice joint.
CONVENIENCE AND SPEED OF INSTALLATION:
Splicing or repairing the belt can be done without removing it from the conveyor, allowing the production process to continue without prolonged downtime.
HYGIENE:Mechanical joints can interfere with belt cleaners, which may affect the cleanliness of the belt; vulcanization, on the other hand, leaves a seamless, smooth surface that enhances the efficiency of belt cleaners.
Advantages of Mechanical Splicing Using ALLIGATOR Locks (FLEXCO)
STRENGTH:The mechanisms are made from galvanized, stainless steel, and MegAlloy alloy, and feature specially shaped teeth that deeply penetrate the belt carcass. The connecting rod can be optionally chosen from steel or stainless steel wire, nylon-coated, or spring wire made of stainless or ordinary steel.
DURABILITY:
Resistant to impact loads, contributing to a long operational life.
CONVENIENCE AND SPEED OF INSTALLATION:
Mechanical splicing is installed on the conveyor belt without dismantling the equipment. The clips are positioned along both ends of the belt and quickly connected with a steel rod.
Yes, of course. Our specialists can come to your production site and perform the splicing without the need to dismantle the conveyor.
No, the partitions and corrugated sidewalls are welded onto the belt and are not removed during the entire subsequent period of operation.
Both methods are reliable. The only difference is that, with hot vulcanization, a monolithic smooth surface remains, which promotes more effective interaction with the belt cleaners.
This is to prevent the product from spilling or falling off the edges of the conveyor belt during transportation.
The dividers capture bulk and chunk materials and help lift or lower them along the conveyor.
A conveyor belt with corrugated sidewalls and dividers allows for the transportation of cargo at a significant incline (up to 60°). A conveyor belt with dividers in the form of bucket-shaped grips can increase the incline angle up to 90°.