An elevator that had been idle for over a year successfully resumed operation with minimal expenses. Thanks to the modernization carried out, the facility achieved a throughput of at least 50 tons per hour.
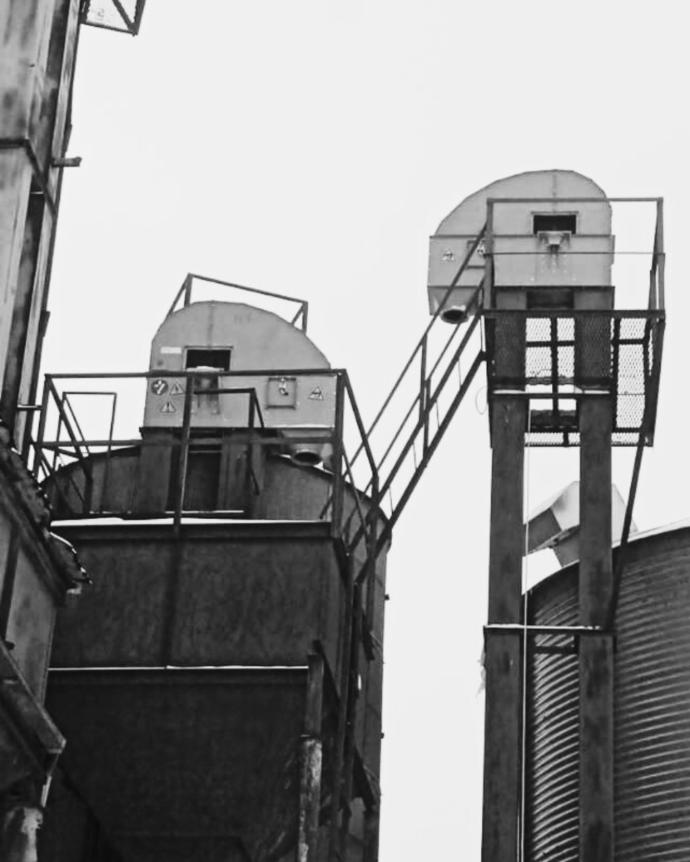
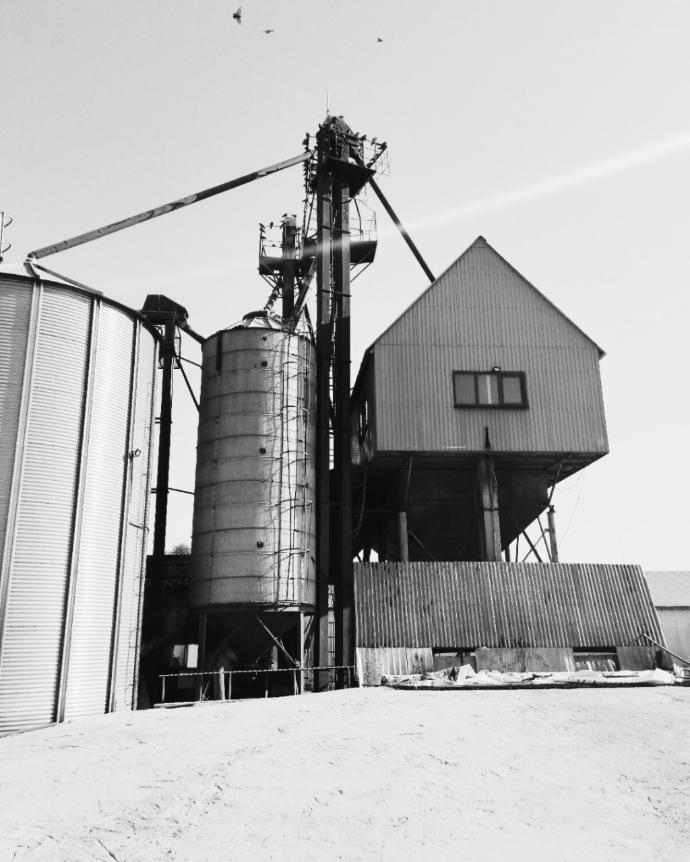
Key Stages of the Work
During a technical inspection, specialists identified a number of critical upgrades necessary for the stable and safe operation of the elevator. The main measures included:
- Replacement of bucket elevator heads;
- Complete refurbishment of three chain conveyors;
- Reconstruction of the gravity flow system with adjusted slope angles;
- Restoration of grain cleaning equipment;
- Replacement of the pit cover;
- Renovation of the conical wooden floor of the silo.
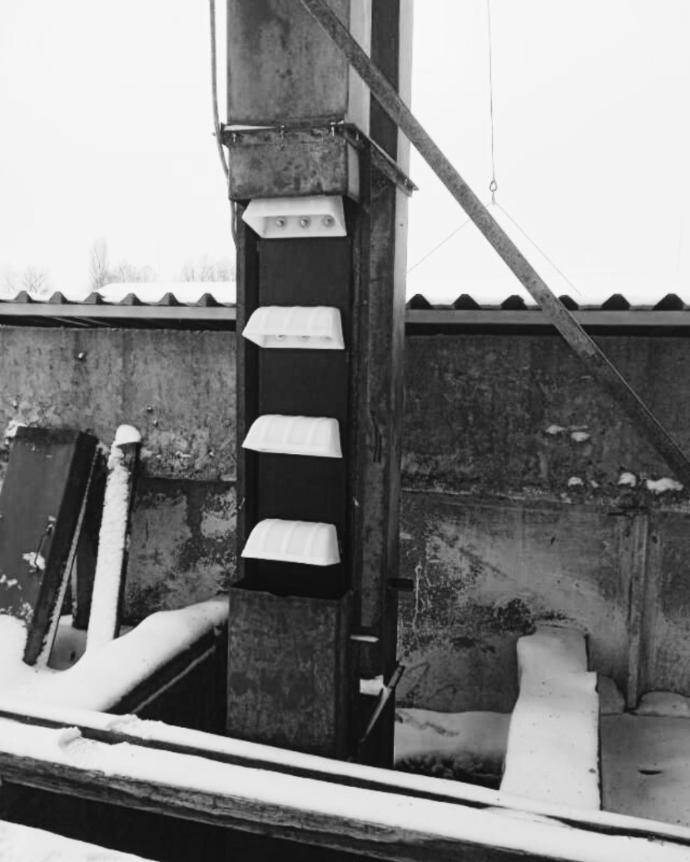
Technical Solutions and Innovations
As part of the project, all necessary components were manufactured and installed directly on-site. Additional work included:
- Installation of new equipment control panels;
- Upgrade of the lighting system;
- All conveyors were equipped with sensors for safe and uninterrupted operation.
To ensure high reliability and durability, components from leading global manufacturers were used: John King chains, STIF belts, and motor reducers from European brands.
We successfully restored the operation of the grain elevator within a short timeframe and on a minimal budget, ensuring stable performance. The use of modern technological solutions and high-quality components made it possible to achieve maximum efficiency with optimal costs.
After the completed work, the elevator was put back into operation and its seamless performance was ensured. The project has become a successful example of effective modernization with minimal investment and high productivity.
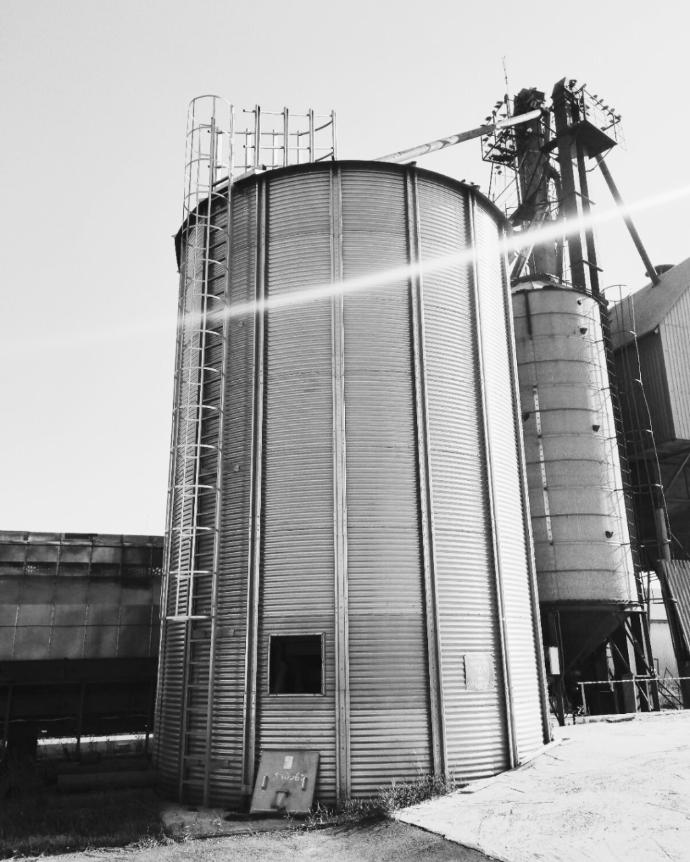
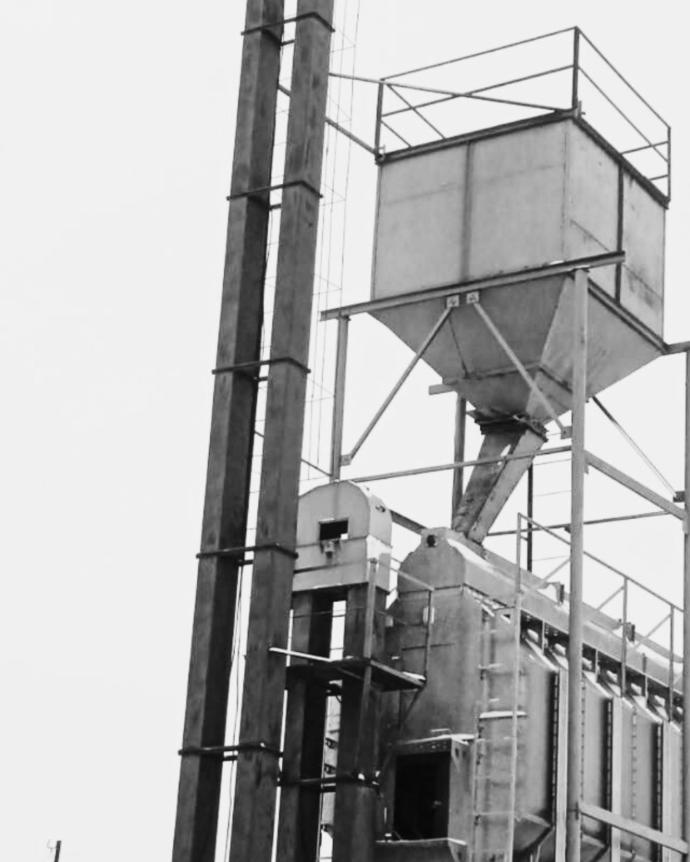